My interest in making a violin dated back to when I was at school. I loved woodwork and we had a workshop in the school and our teacher was an excellent tradesman. He started making violins as a sideline and I was smitten from that day forth.
Many years passed before I realised my dream and at about 50 I decided to have a go. Good violin makers will spend between 100 and 150 hours making one instrument by hand. I took longer. I got some support from Cambridge violins makers during the process.
The first issue was to plain down the ribs ( the sides of the violin ) to a thickness of 1 millimetre. Maple is the traditional wood which then had to be bent round a hot metal iron spike to bend into shape. You have to do it carefully to stop the wood burning or splitting.
I used a template frame the shape of the violin and bent my newly folded ribs around the shape. This template would eventually be removed once I had blocked out the corners with maple wedges.
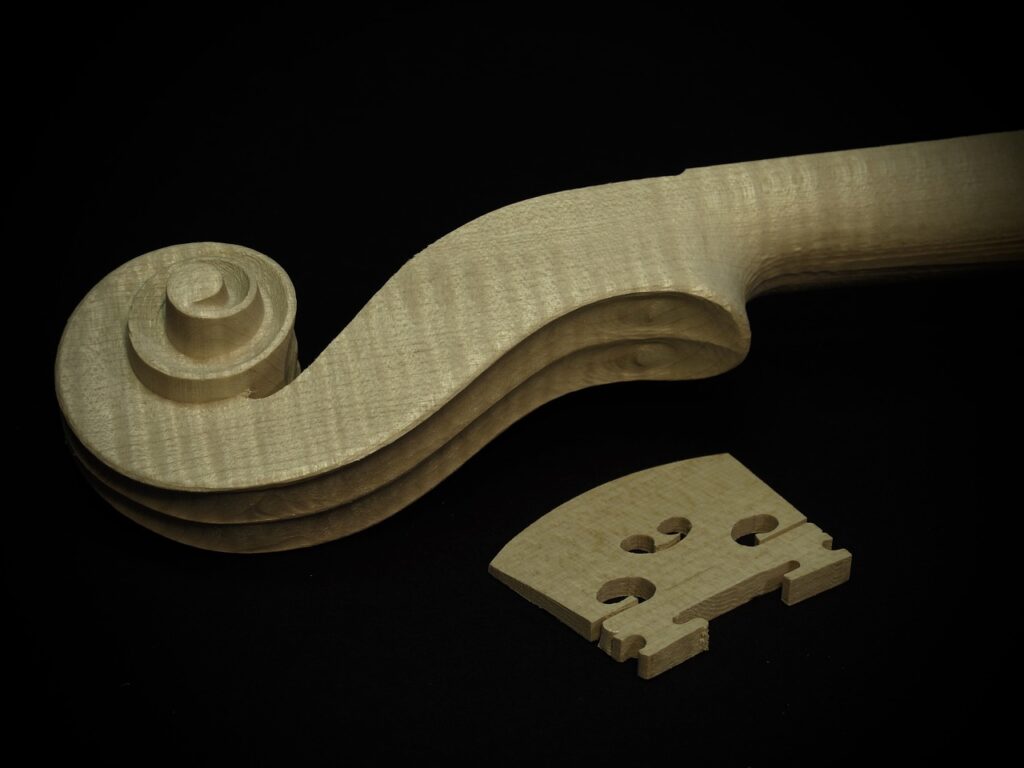
Then came the scroll, also in maple which I cut the rough shape with a saw and then shaped with gauges. The scraper finished it off. This took a great deal of time but once completed I was pleased with it. Now it was time to do the back which is also of maple and is the base of the violin. This had to be shaped and gauged out on both sides. This was followed by the use of tiny finger planes that took out the tiny gauge marks. Finally the whole back was finished with a scraper ( No sandpaper )
Next was the belly , the front of the violin which was in spruce for flexibility. Although the wood was softer you had to be very careful with the gauging as it was easy to split the wood. The rest of the belly followed the back in technique and all parts of the depth were measured with callipers. The f holes were cut with a coping saw.
The ebony strip that surrounds the parameter was very fiddly as a small strip had to be chiseled out to implant the wood. All the instrument was glued together with animal glue which had to be heated up, The fingerboard etc was also made of ebony. Varnishing and finishing is for another time.
Peter Bull( Author of the get in touch series )